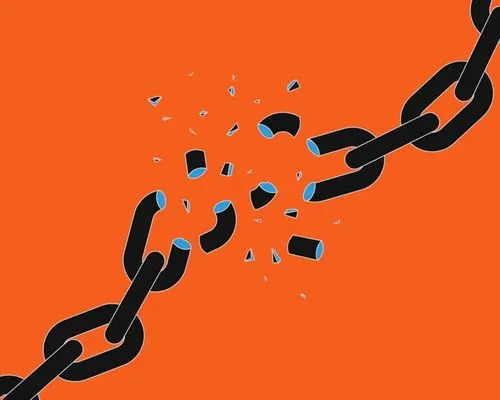
Your business depends on completing energy projects on time and on budget. But supply chain disruptions are making it harder to meet these goals.
No doubt you’ve found it more difficult to acquire transformers and other necessary materials in recent months. And believe me, you’re not the only one. Before 2020, lead times for transformers were 8-10 weeks. Today, many providers have lead times that run for 36 to 40 weeks—assuming they give you a quote at all.
Why is this happening? What’s causing these product shortages in the electrical market, and what can you do to avoid delays in getting what you need?
What’s happening to supply chains?
Economic growth depends on a stable and well-functioning supply chain, the chain of production and distribution that puts goods in the hands of consumers and other businesses. It’s how we get everything from electrical steel and computer chips, to oil and natural gas, to food, to basic consumer goods (cars all the way down to paper, ink, and lightbulbs).
Today, we’re seeing massive delays in supply chains, which is weakening and eroding the global economy. It’s getting harder to get what you need when you need it, not just in the electrical market, but almost every market.
Here’s a recap from IHS Markit’s recent webinar on the supply chain crisis.
The globe is experiencing supply chain constraints and delays that haven’t been seen since World War II.
A record number of companies report that their supply chains are being stretched and that they cannot get the materials they need when they need them.
We are now in the third month of record-breaking price increases. The delays are only getting worse at this point, and now, all suppliers are driving their prices up.
Global economic forecasts are trending downward as profit expectations drop. More and more companies are finding that they cannot simply pass on the costs of business to consumers.
The deepest crisis is in the shipping container industry, and there are no signs of the log-jam breaking. There are enough boats and trucks—just not enough places to ship and not enough labor to move things.
Spending patterns have changed dramatically over the past two years. More people are opting for e-commerce over bricks-and-mortar, which has only increased shipping demand.
Every shock to the system (a lockdown, a travel ban) backs up the supply chain even more, compounding the problem over time.
Predicting when goods will arrive at their destination is now 30% less accurate.
The chart below, taken from the IMF blog, shows how drastic today’s delivery delays are.
“To calculate the index, purchasing managers are asked if their suppliers’ delivery times are, on average, slower, faster, or unchanged compared to the previous month. Readings above 50 indicate faster delivery times, readings at 50 signal no change, and readings below 50 indicate slower delivery times compared with those of the prior month.
The recent sharp drop in the delivery times index reflects surging demand, widespread supply constraints, or a combination of both. During such times, suppliers usually have greater pricing power, causing a rise in prices. Moreover, these supply chain delays can reduce the availability of intermediate goods which, combined with labor shortages, can slow down production and output growth.”
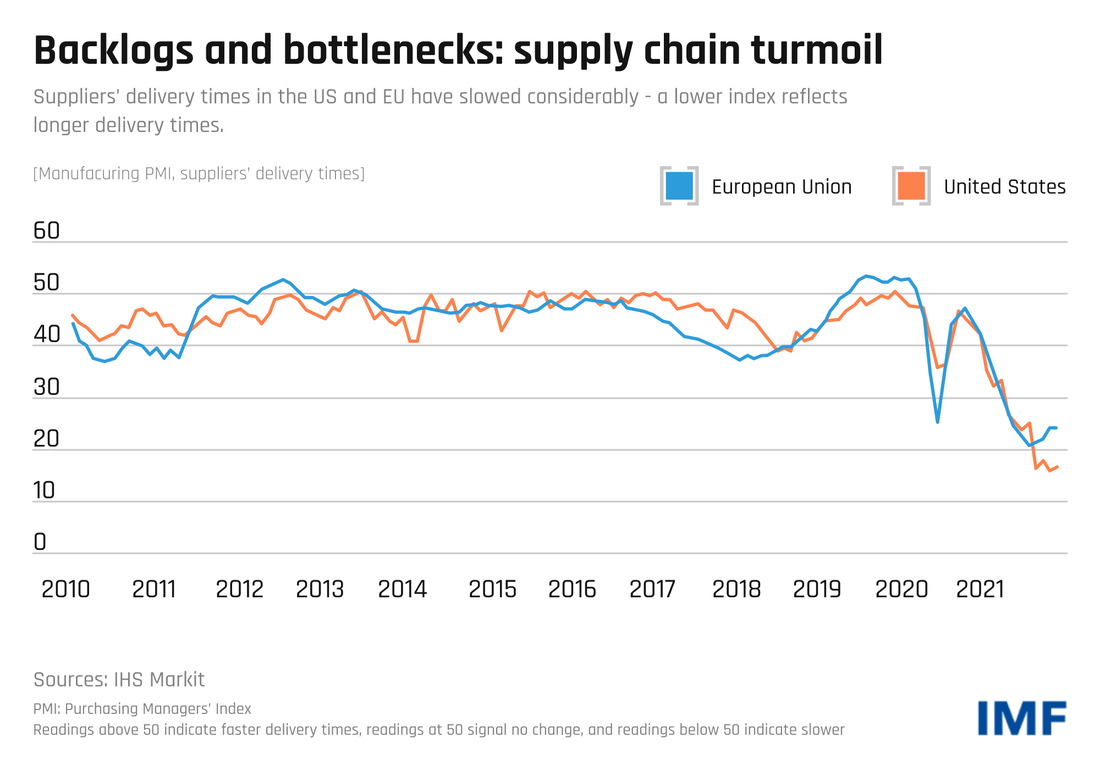
What’s causing the delays?
The electrical market supply chain (and every other supply chain, for that matter) is being disrupted by two ’demics.
First, the COVID-19 pandemic (and our response to it) interrupted the supply chain in many ways. Manufacturers, distributors, and shipping companies ground to a halt for months when governments implemented severe restrictions on global and domestic travel to slow the spread of the virus. Regardless of the effect of these measures on stopping the virus, they certainly slowed down economic growth.
This shouldn’t be surprising. If you stop production of goods and shut down a massive, highly interconnected machine consisting of dozens or hundreds of moving parts, it takes a long time to get it going again. But we’re not even out of the “disruption phase” because many countries are still restricting travel. Today, there are shortages in raw materials and finished goods across the board. And even when there is a large supply of the goods you need, you often can’t get them.
The second ‘demic is the widespread labor shortage—the sansdemic. While “pandemic” means “all people,” “sansdemic” means “without people.” We just don’t have enough people to fill jobs. When supply chain jobs go unfilled, we can’t run global or domestic supply chains as efficiently as we used to. And the problem isn’t going away anytime soon.
Back in May, labor market economists started talking about three factors that are contributing to this sansdemic:
The largest generation in American history, the Baby Boomers, are retiring. Many were already planning to retire before 2020. But retirement rates spiked to record highs because people were tired of work disruptions or were afraid of catching the coronavirus. The problem for us is that many of the people retiring aren't at retirement age yet and are leaving hard-to-fill senior positions. Replacing them won’t be easy.
The two generations that followed the boomers, Gen X and the Millennials, are smaller and have much lower labor force participation rates (the percentage of the working-age population that is working or is interested in work) than the boomers. For example, nearly 90% of working-age boomer men worked. In 2021, the male LFPR plummeted to a staggering 67%, leaving many jobs unfilled.
The American birthrate is as low as it has ever been—there are simply fewer babies being born. This means that the sansdemic isn’t going away anytime soon. Steady labor markets require a steady supply of workers. The worker supply is anything but steady right now.
Two key ways to deal with shortages
This market disruption is here to stay for a while—decades, most likely. But you probably don’t need supplies for projects 20 years from now. You need supplies today. So, if you’re a company or a contractor that just needs to get a project done, how can you minimize the effects of supply chain disruptions?
How can you get what you need when you need it?
Procure materials sooner
Procure your materials sooner in the project planning process. When you need a transformer, you tend to need it yesterday. Many transformer companies have their own supply chain issues, making it difficult to purchase from them within the timeframes you may be used to. Not only that, but the companies that have lots of inventory (like Maddox) are in high demand right now, meaning their inventory will be depleted faster. So the earlier you acquire your materials for a project, the more likely you’ll have your materials when it’s time to use them.
Develop with flexibility
Second, try to develop projects with specs and configurations that are flexible enough to execute with the materials available to you. Sometimes customers call us with very tight or highly specific needs, which are always more difficult to meet. Not impossible, of course (we do our best to be flexible too!), but more difficult. If you have more wiggle room in terms of product dimensions, you can get what you need much sooner.
Summary
The pandemic and the sansdemic are disrupting global and domestic supply chains. This means that in almost every market, including the electrical market, it’s harder to acquire the materials you need for a given project. And this problem isn’t going away anytime soon. As older generations retire, younger generations work less, and fewer babies are born, supply chain jobs are going to go unfilled. We need to brace ourselves for supply chains that are less efficient than they used to be.
To avoid delays in material acquisition, you should focus on A) procuring materials earlier in the project planning process and B) being flexible based on the materials and goods that are available to you.
In the market for a transformer, or think you might be in the future? Reach out to Maddox today. And if you want to see more content like this, subscribe to the Maddox newsletter.