Updated DOE 2029 Energy Efficiency Standards for Distribution Transformers
In April, the DOE updated its transformer efficiency standards. Three main areas of improvement: extended timeline, core steel requirements, & cost savings.
November 1, 2024
News
In 2023, the DOE shared its 2027 proposal for transformer efficiencies. Like the previous standards, the update would affect all new built transformers. The proposal included significant improvements for transformer efficiencies. But, these higher efficiencies would have required equally significant manufacturing changes. With factories already strained to meet demand, these proposals received some pushback. (What's causing long lead times and how you can beat them.)
This prompted revisions.
On April 4, 2024 the DOE revised their 2027 proposed standards. These revisions offer relief to transformer manufacturers. Three main improvements are:
- Core steel requirements
- Cost savings
- Extended timeline (2027 vs 2029)
Let’s compare this newest version with the 2027 proposal.
Updated Efficiencies
The proposed 2027 standards aimed to increase efficiency by around .16%. The goal of these standards was greater energy savings and emissions reductions. But, this would have required up to a 50% reduction in losses.
These standards provoked swift pushback. See our article on last year’s standards for more details.
Less Stringent Requirements
The finalized standards require a reduction in losses between 10% and 30%. (These percentages are in comparison to DOE 2016.)
Liquid-Filled Transformer Reduction in Losses:
- Single-Phase ≤ 100 kVA: 5%
- Single-Phase ≥ 100 kVA: 20%
- Three-phase ≤ 500 kVA: 5%
- Three-phase ≥ 500 kVA: 20%
Dry-Type Transformer Reduction in Losses:
- Low Voltage Single-Phase: 30%
- Low Voltage Three-Phase: 20%
- Medium Voltage: 20%
This is the “maximum improvement in energy efficiency that is technologically feasible and economically justified” (p. 9). The tables below contain the new efficiency values.
DOE 2029 Standards
Low-Voltage Dry-Type Standards (<600V)
Medium-Voltage Dry-Type Standards (>600V)
Liquid-Filled Standards
Impact on Manufacturing
These less stringent efficiency requirements provide relief for OEMs. The impact on current manufacturing processes is less severe. In addition, factories have more preparation time to enact the new standards.
Core Steel Requirements
Most distribution transformers have a distributed gap core design made with grain-oriented silicon steel. It’s cost effective to build, and provides high efficiency ratings. The 2027 proposal would have required an amorphous design for nearly 90% of cores. But, there is only one supplier of amorphous steel in the U.S. A predominantly amorphous design would demand an extensive restructuring of core steel supply chains. Not to mention amorphous cores are significantly more costly.
This would have forced a huge restructuring of manufacturing processes. The strain would have been enormous.
The new standards allow 75% of cores to use grain-oriented electrical steel (GOES). Most of this can come from U.S. factories. Manufacturers will not need to completely overhaul their processes for DOE compliance.
Two-Year Extension
The DOE's original timetable for implementation was very short. Manufacturers would have only had four years to comply.
The DOE has now extended the compliance deadline from 2027 to 2029. This makes compliance with the new standards far more feasible. Factories have more time to plan for the changes they will need to make.
Added kVA sizes
DOE 2016 regulation included kVAs up to 2500. The new update covers sizes up to 5000 kVA. Manufacturers will now have to incorporate these standards for larger units.
Costs vs. Benefits
As mentioned, these revisions require manufacturers to retool their factories and bring their products into compliance with the standards. The DOE estimates the following costs to transformer manufacturers for this nationwide overhaul:
- Liquid-filled distribution transformers: $187 million
- Low voltage dry-type transformers: $36.1 million
- Medium voltage dry-type transformers: $5.7 million
Despite their cost, the benefits of the final standards are significant. The new efficiencies are estimated to save Americans over $14 billion over 30 years. Last year’s proposal would have also cut long term energy costs. But, the hidden cost was the strain it would have placed on manufacturers.
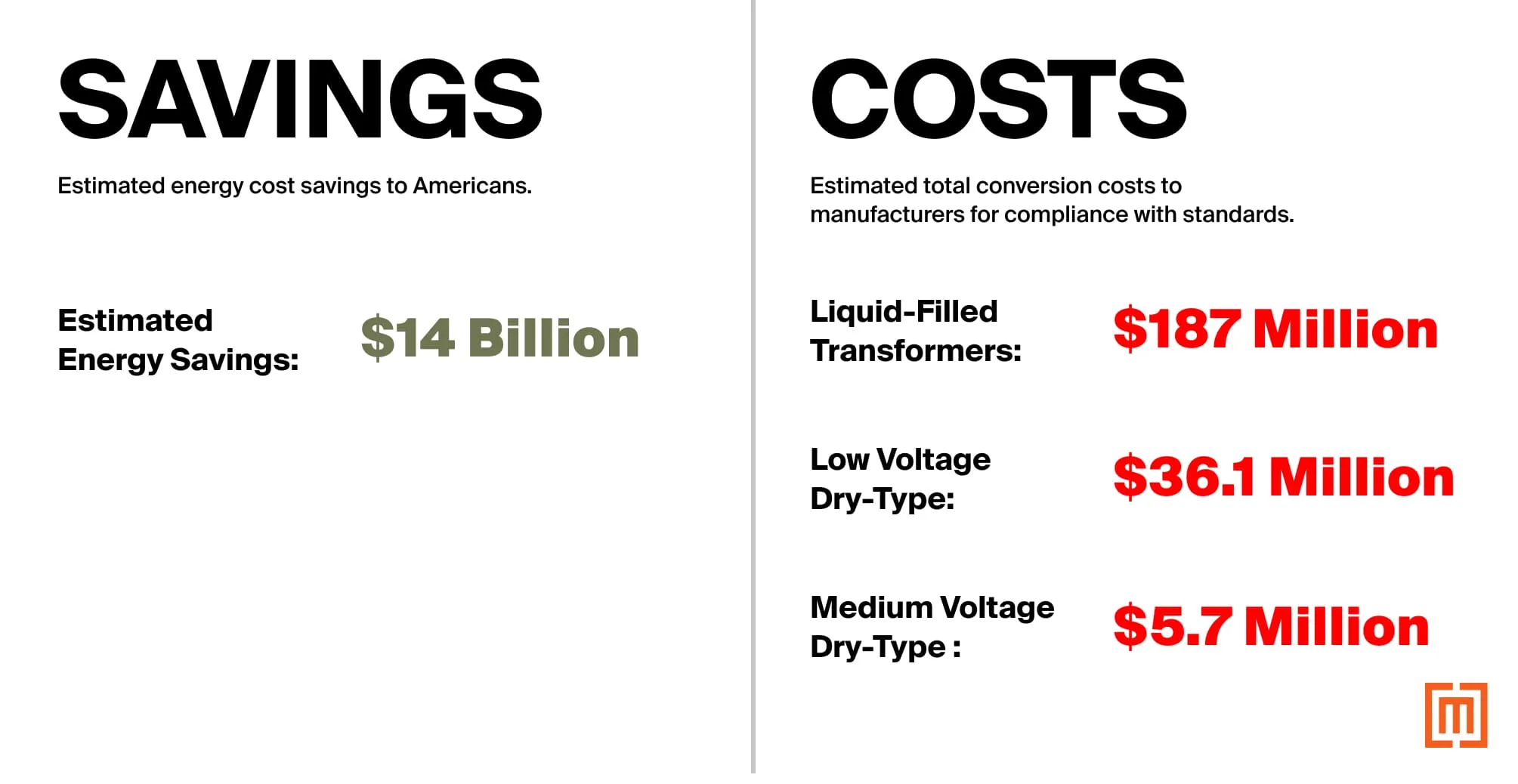
Conclusion
The electrical industry faces significant challenges in the coming years. Supply chain delays caused by raw material shortages aren’t going away. The new DOE efficiencies are realistic about these challenges.
Here at Maddox, we’re doing everything possible to help ease these challenges. If you want to learn more, check out our transformer remanufacturing program. Or, fill out the form below for more information.