Transformer oil
Oil cools a transformer's windings. Types of transformer oil include mineral oil, FR3® fluid, and silicone oil. Find out which is best for your transformer.
March 31, 2023
How To's
Oil-filled transformers across the United States are powering our nation's economy. The smooth operation of these transformers is largely dependent on the quality and condition of the oil inside each unit. Transformer oil is specially designed to have both high thermal conductivity and high dielectric strength for cooling, and insulation. In this article, we will cover the purpose of transformer oil, the most common types of oil, and which type you should use in your transformer.
The Purpose of Transformer Oil
Cooling
The oil in a transformer tank cools the windings through natural convection. The hottest spots in the transformer tank are located in and around the transformer windings, and as a result, the fluid in and around the transformer core and coils will be warmer. This warmer, more buoyant, fluid around the windings migrates out toward the less buoyant fluid spaces in the tank, dissipating heat from the core and coils. In larger transformers, the warmer fluid moves through radiators where heat is transferred off into the ambient air. As the fluid in the radiators cools, it is pushed back towards the windings by the warmer fluid circulating through the tank. The cooler fluid heats up again as it moves closer to the center of the tank near the windings, and the process is repeated as shown in the image below.
(Learn more about transformer cooling and cooling classes)
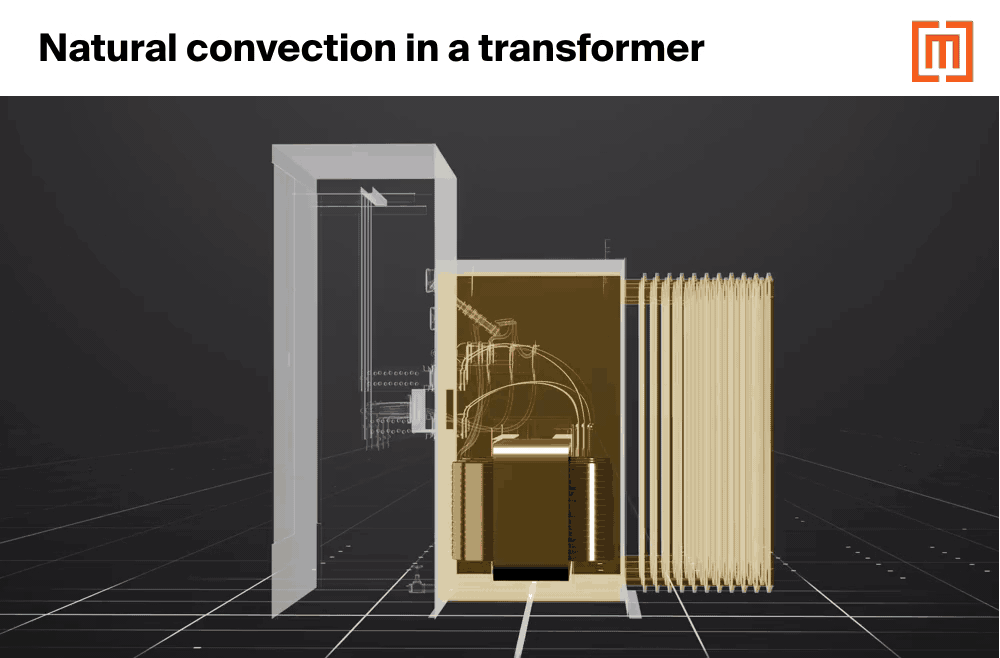
Electrical Insulation
Transformer fluid plays a key role in the insulation system of transformers. Transformer windings are insulated by a working relationship between paper (composed of cellulose) and fluid. The combined action of the paper insulation and fluid provides the dielectric strength required for safe and effective transformer operation. A high dielectric strength means the insulating material will maintain its integrity when exposed to a strong electric field. The total dielectric strength of the insulating fluid is measured by the maximum voltage required to produce a failure in the insulation medium–called a dielectric breakdown voltage. The dielectric breakdown voltage will always be significantly higher than the rated voltage of the transformer windings to ensure the transformer’s insulation system is effective for service. In the factory, dielectric tests are performed to certify the integrity of the insulation such as impulse and short circuit.
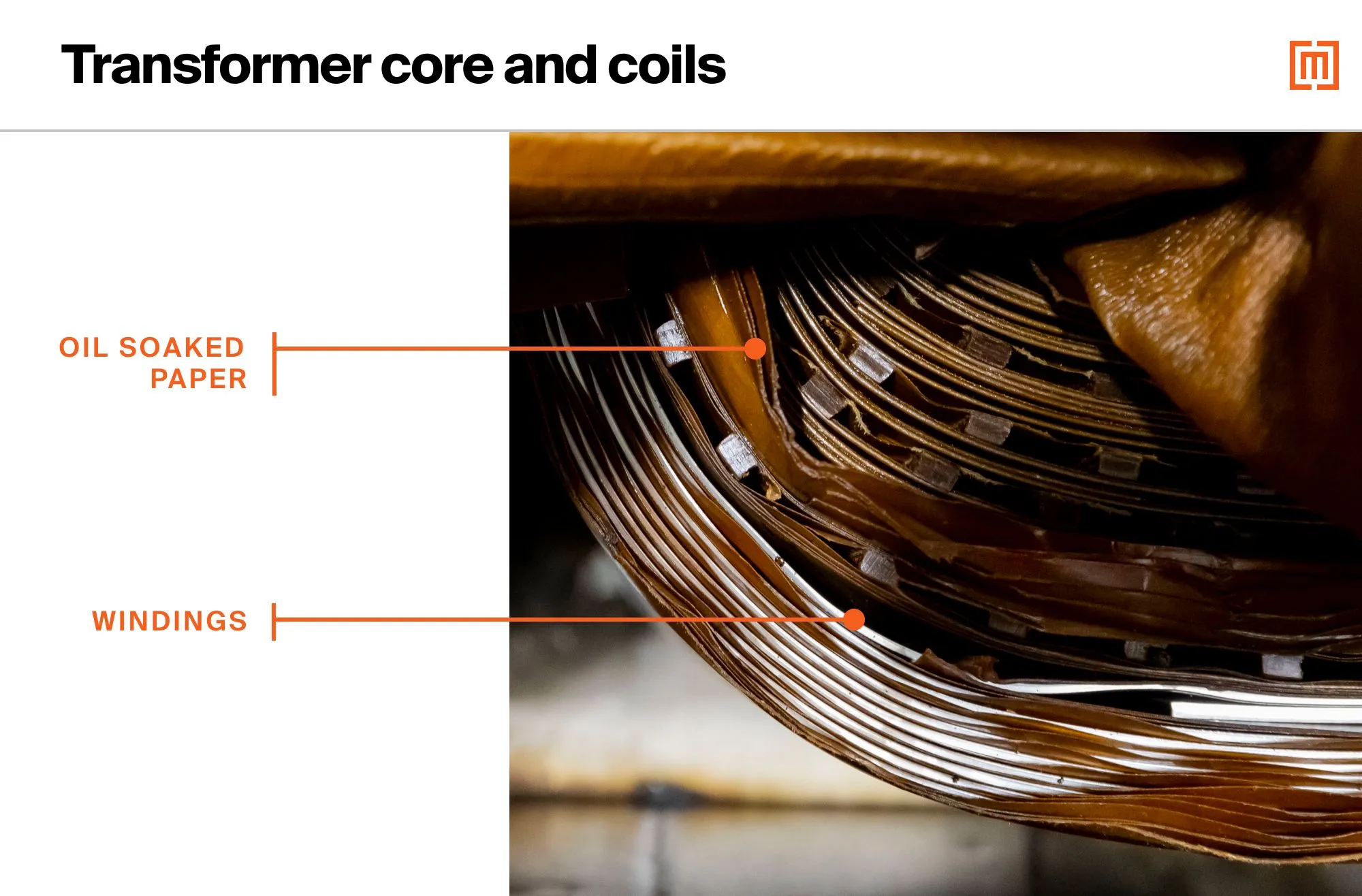
Lubrication
Many oil-filled padmount and substation transformers house devices such as tap changers or load break switches. These devices are immersed in the transformer’s dielectric fluid, and they are designed to be operated in oil. For this reason, the transformer fluid must provide a satisfactory means of lubrication for these devices. The fluid must facilitate smooth operation for moving components and prevent locking up or seizure between contact points.

Types of Transformer Fluid
There are several different types of fluids on the market today used in transformers. Of the fluid options available, the three most common are:
- Mineral Oil
- Natural Ester Fluid (FR3® fluid)
- Silicone.
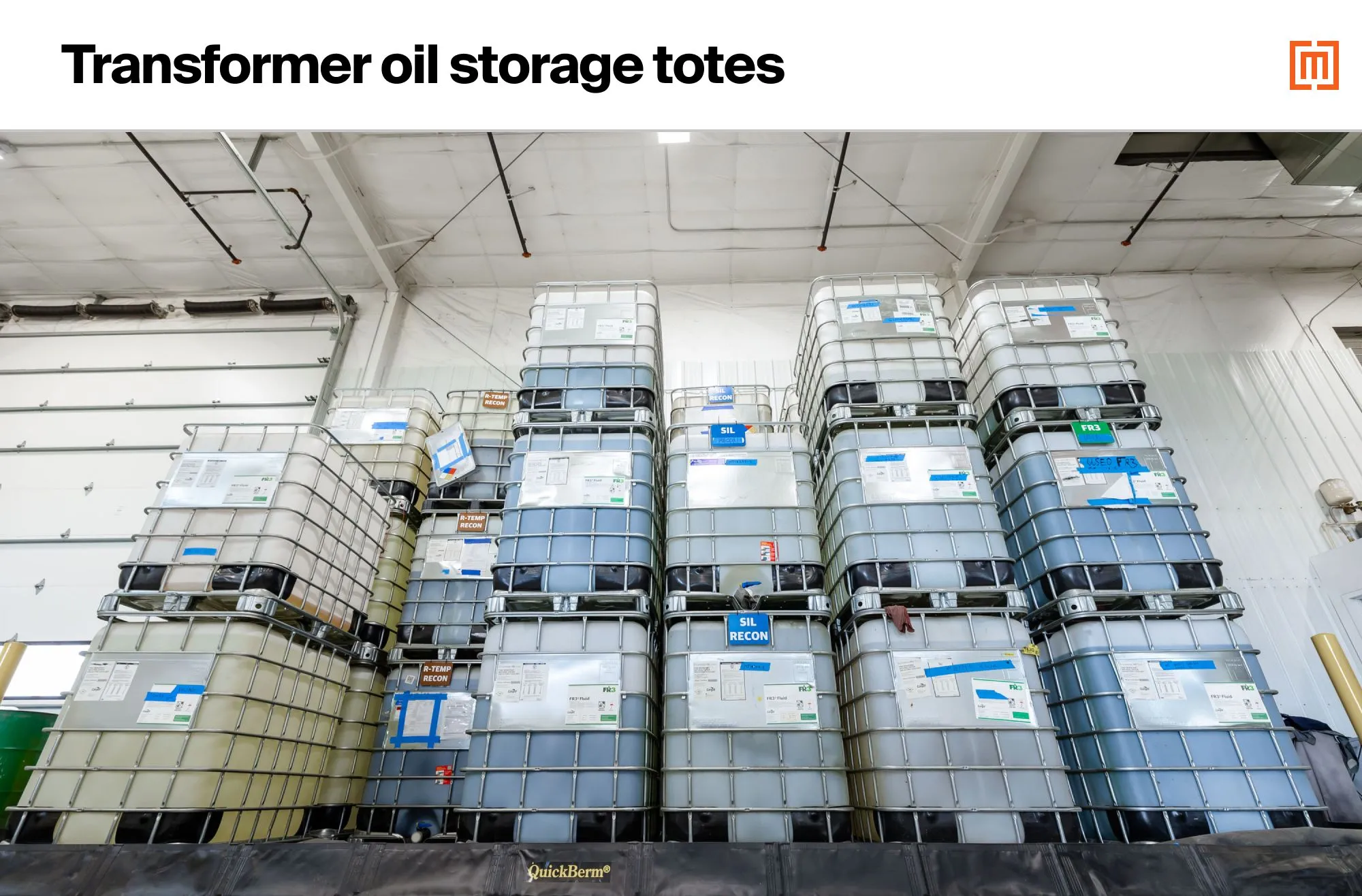
Mineral Oil
Mineral oil is a hydrocarbon-based fluid that is distilled from naphthenic-based oils. It has been the go-to fluid for transformers for many years, which is why there is more performance data available on it than any other fluids on the market to date. Mineral oil has a low viscosity which makes it an effective fluid for cooling by natural convection.
Mineral oil’s fire point is around 165 degrees C which does not qualify it as a suitable fluid for applications requiring a “less flammable fluid”. Transformers filled with mineral oil will bear an ONAN cooling class designation (the “O” designating a fluid with a flashpoint below 300 degrees C) Most mineral oil options contain an inhibitor to improve oxidation stability and reduce the buildup of sludge inside the transformer tank. The presence of this inhibitor is for the most part standardized across the industry and denoted by the prefix “Type II”.
Natural Esters (FR3® fluid)
Originally developed to provide a more environmentally friendly version for higher flashpoint fluids, natural esters are now the go-to for applications requiring a less flammable fluid-filled transformer. Transformers filled with natural esters bear a KNAN cooling class marking on their nameplate (the “K” designating a fluid with a flashpoint above 300 degrees C). Natural ester fluids are typically seed oil based rather than hydrocarbon-based–like mineral oil.
Several versions of natural ester type fluids have been introduced into the market over the years. The most significant and widely used option in the US currently is FR3® fluid. It is 100% vegetable oil based and fully biodegradable with a flashpoint around 330 degrees C or higher. The use of FR3® fluid in transformers can also enable an additional increase in transformer kVA capacity. Studies have shown that the use of FR3® fluid can also increase the lifespan of a transformer’s insulation system. In a sense, FR3® fluid can dry out the paper insulation around the windings. Moisture near the coils is continually moved away from the windings–and through hydrolysis–converted into mild non-harmful fatty acids–eliminating the harmful effects of moisture build-up in and around the windings.
Learn more about the benefits of FR3® fluid.
Silicone
Silicone is a synthetic fluid that is less widely used in transformers today. Its high fire point makes it suitable for applications requiring a less flammable fluid, however, since it has no biodegradability, natural esters are usually favored where a high fire point is required. Between natural esters and mineral oil, silicone is typically the more costly of the three.
Transformer Oil Comparison
Fluid Comparison
Cold Startup Considerations with Mineral Oil & FR3® fluid
Some transformer installations in cold temperatures will require special considerations as far as transformer fluid is concerned. When energizing a transformer in subzero conditions (below 0 degrees C), it is important to bear in mind that frost and ice will likely be present inside the tank. This moisture could affect the dielectric strength of the transformer fluid.
The viscosity of mineral oil is lower than FR3® fluid and it has a more effective pour point in lower temperatures, but its dielectric strength is weakened with the introduction of moisture in cold temperatures. FR3, however, maintains its dielectric strength much more effectively in colder temperatures. Due to its higher viscosity in colder climates though, FR3® fluid will not be able to move freely through the transformer until the unit warms up under load.
As a result, both mineral oil and FR3® fluid filled transformers will require special startup procedures in colder climates. The recommended cold startup procedures for transformers can be found in IEEE standards C57.12.00, C57.93.00, and C57.106.00.
Check out this article for procedures on transformer startup in colder temperatures.
Polychlorinated biphenyls (PCBs)
Though not an issue with transformer fluids manufactured in today’s market, at one time PCBs were very common in transformer fluids. Their presence in fluids offered a very high flashpoint option for transformers requiring a less flammable rating (such as indoor installations). When it was learned that PCBs were extremely hazardous, their use in transformer oils was banned (1979).
Today, the concern with PCBs in transformer fluids is related to older units in service today that were built around the time such fluids were used. Units with a manufacture date prior to 1980 should be tested to determine whether or not PCBs are present in the oil.
How to test transformer oil
You can test your transformer oil through a Dissolved Gas Analysis (DGA) test which has long been the most reliable and accurate method for determining the internal health of oil-filled transformers. The analysis requires drawing an oil sample from the unit, extracting the gasses from the sample, and analyzing the gasses through gas chromatography. The results of the chromatography tell the lab about different problems that may be arising inside the transformer.
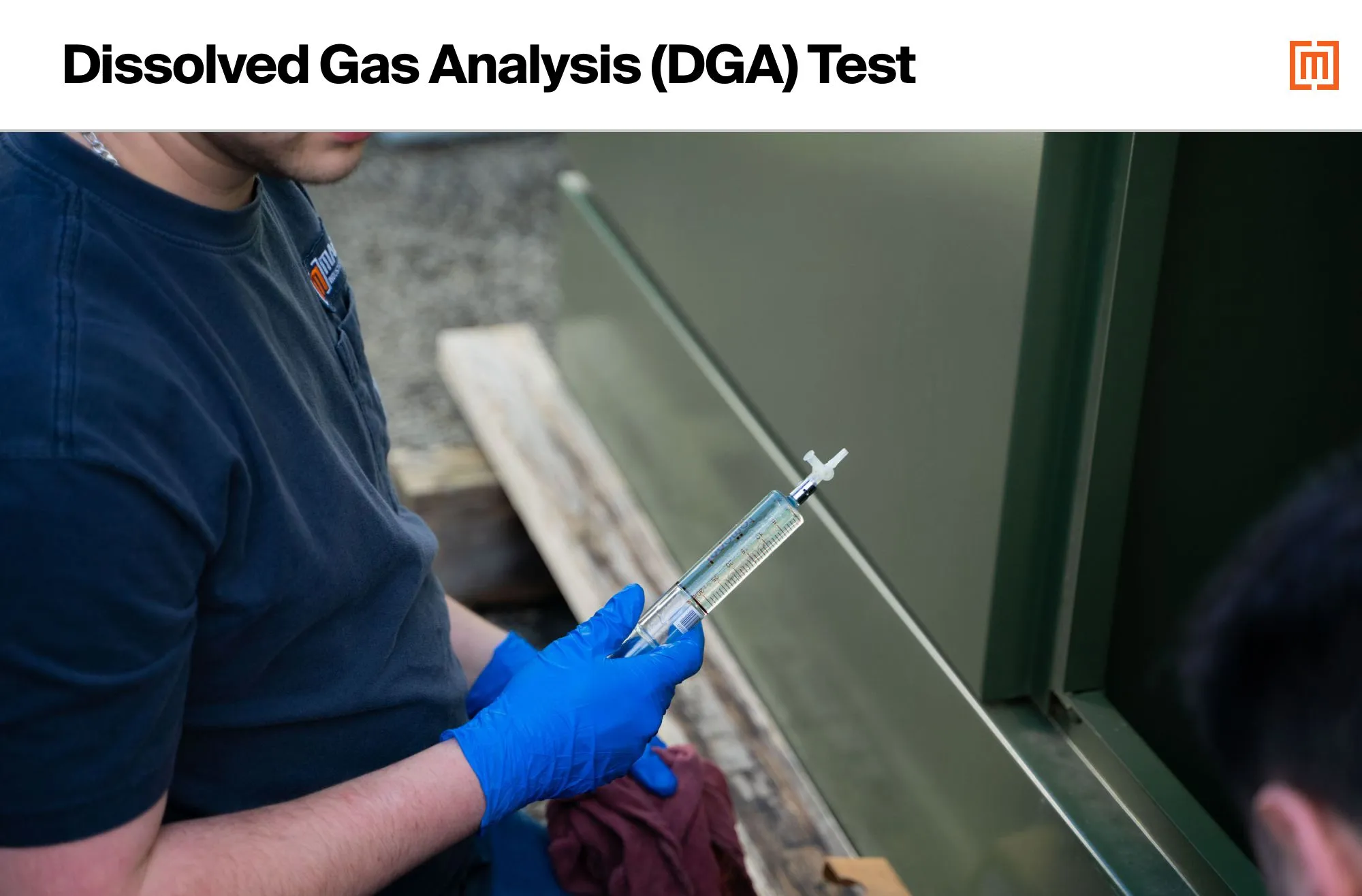
Which oil type should you use in your transformer
Which fluid you use depends on what is most important to you, cost, environment etc.
If you are looking for a low cost fluid, mineral oil is a dependable solution, and may be the best option. On the other hand, for indoor applications, less-flammable requirements, and biodegradability, natural esters (FR3® fluid) are the ideal choice.
Whatever you need, Maddox can help you find the solution. Give us a call for a quote.